Production managers are faced with dozens of decisions when figuring out how to best run their packaging operation. Sometimes, the options may seem overwhelming, but with enough information about each choice, informed decisions about the best way forward are possible.
One choice that managers need to make when choosing a side seal wrapper is whether to use a 2-belt or 3-belt wrapper for sealing packages.
2-Belt Wrapper
With just infeed and exit conveyers, the 2-belt design is a popular choice among smaller manufacturers for its affordability and compact machine size. This compact size uses very little floor space and will allow end users to run infinite length products. However, with the 2-belt design the products must be spaced apart before entering the wrappers infeed conveyor, adding time, energy, and potential for error. With the side seal being made after the cross seal you may experience several scrap breaks.
3-Belt Wrapper
This choice has a third conveyer belt specifically for sealing, and many feel that the outcome is well worth the added space and cost. All three belts are independently controlled, allowing more flexibility, and ease of use. Three-belt wrappers are recommended when the product is particularly short or tall, as gaps can be smaller, and the film does not have to be pulled directly to the cross seal. Extra-long items also work best in a 3-belt design, because products can be cleared from the exit belt immediately instead of waiting for the next package to come through. Other benefits of the three-belt system are a narrower scrap tail, which saves both film and cost, no scrap breaks, and the ability to use the auto-space feature.
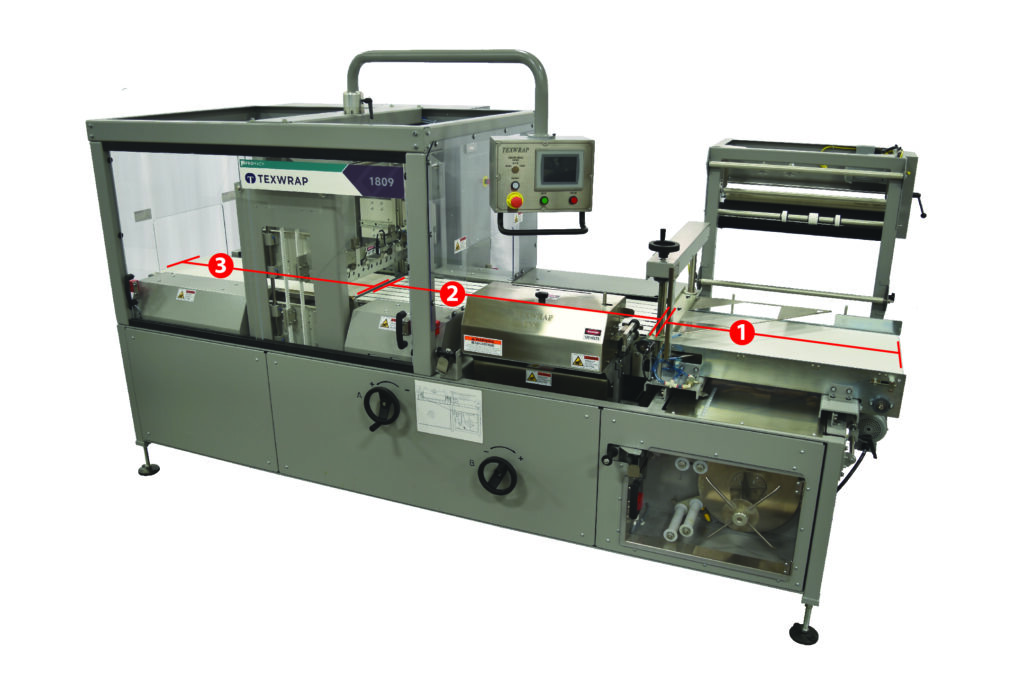
The Consensus
Among manufacturers it’s generally agreed that accommodating the extra cost and room for the 3-belt system is the way to go. Neither design is a bad option, but if you are looking for an efficient, easy to use side seal system that is flexible to all shapes and sizes of product, the 3-belt design is significantly better.